Refractory Solutions for Aluminum Melting Furnaces
The aluminum melting furnace has a full castable structure and a castable mixed refractory brick structure. Castables and refractory bricks are also selected according to different parts. When the aluminum melting furnace is running, the material is extremely permeable. It is easy to soak the refractory and react with it, causing the volume of the refractory to change, gradually causing cracks and damaging the surface of the refractory. Refractory manufacturers, in response to these problems of customers, proposed solutions for refractory materials for aluminum melting furnaces. I hope it will help you when choosing refractory materials for aluminum melting furnaces.
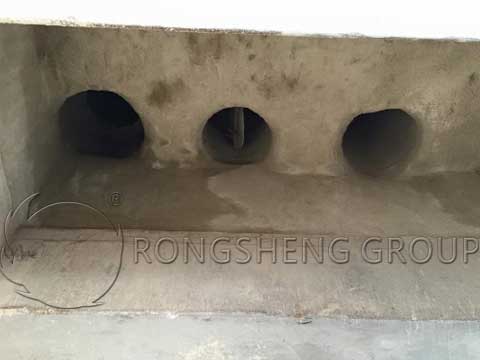
Causes of Damage and Cracking Caused by Refractory Materials Used in Aluminum Melting Furnace
- 1. The aluminum water will penetrate into the pores or small cracks of the refractory material, and gradually cause the refractory material to crack and fall off the structure. Moreover, once the construction personnel fail to discover the problem in time, it will slowly cause the entire refractory material to be penetrated and corroded. In addition, aluminum and its alloys are prone to physical and chemical reactions with impurities in refractory materials. The substances produced during the reaction will seriously affect the quality of aluminum products.
- 2. The internal molten aluminum reacts with the refractory material to adhere to the material, forming surface nodules, protrusions and deposits. Once this happens on the surface of the refractory lining, it is difficult to clean. Therefore, mechanical cleaning methods are generally selected. This cleaning method will also have a great impact on refractory materials.
- 3. During the production process of the aluminum smelting furnace, mechanical operations such as charging and cleaning the slag will cause serious wear of the furnace shell, furnace wall, furnace bottom, etc.
Solutions for Damage and Cracking of Refractory Materials for Aluminum Melting Furnaces
If you want to solve the phenomenon of damage and cracking caused by refractory materials used in the aluminum melting furnace, the following measures need to be taken.
First, increase the density of refractory materials and reduce the porosity of the materials. If the refractory has high density and low porosity, it can effectively prevent the penetration of aluminum and its alloys.
Second, improve the resistance of refractories to aluminum water erosion. Excellent resistance to aluminum water erosion, can effectively prevent aluminum water from penetrating and prevent aluminum water and aluminum slag from adhering. The SiO2 and impurities in the refractory can easily react with the α-Al2O3 and Mg in the liquid aluminum, and cause the volume change of the refractory. It causes the refractory to form cracks and accelerates the corrosion of the molten aluminum to the refractory. Therefore, the higher the aluminum content of the refractory material, the higher the purity, the less likely it will react with molten aluminum, and the better the corrosion resistance. At the same time, additives such as barium salt and chromium salt can be added to react with aluminum water to form a protective layer to increase the corrosion resistance of refractory materials.
Third, improve the wear resistance of refractory materials. The wear resistance of refractory materials is mainly to improve its strength, which can effectively improve the wear resistance and mechanical impact resistance of refractory materials.
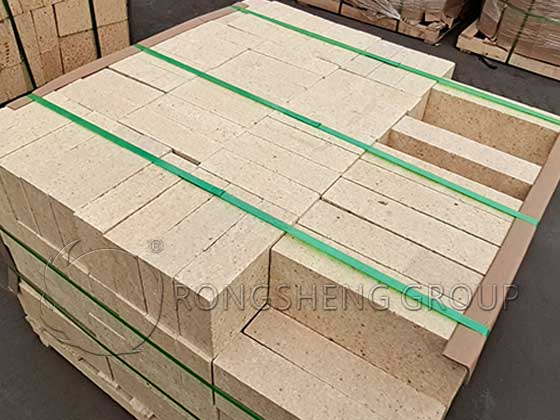
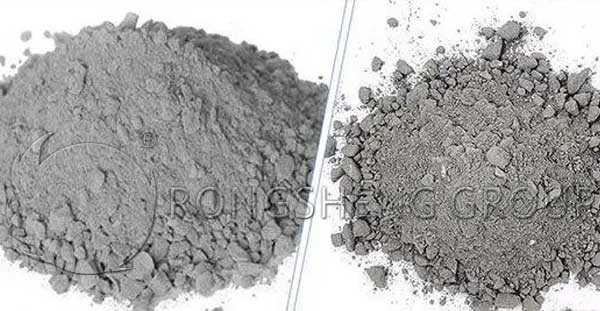
Precautions for Selecting Refractory Materials for Aluminum Melting Furnace
If you want the aluminum melting furnace to operate effectively, you must choose a refractory material that fully meets the boiler’s use when choosing refractory materials. Next, let’s understand the precautions for selecting refractory materials for the lower aluminum melting furnace.
The design of refractory materials for the lining of aluminum melting furnaces should be reasonable, and the refractory materials must fully consider the differences in the side wall of the molten pool, the working conditions of the furnace bottom and the load changes, and the specific structural design is more reasonable.
- 1. Adopt a new metallurgical furnace casting method, integral casting. The pouring method makes the aluminum melting furnace have good overall structure, no brick joints, not easy to leak, and not easy to crack, so that the furnace can run stably for a long time. Long service life. Based on many years of experience in the production and construction of large-scale aluminum melting furnaces, a number of new technologies are used for design and construction, such as “segmented” pouring, the use of convex and concave locks between blocks, and the reasonable setting of expansion joints. These effective construction techniques can ensure the service life of the aluminum melting furnace.
- 2. The masonry process using refractory bricks and refractory castables is the most suitable masonry method used in the masonry process of lining refractory materials in the aluminum melting furnace. It is integrally cast with high-performance non-stick aluminum castable below the liquid level. Long-term use can greatly reduce furnace cracking and aluminizing. High-alumina refractory bricks are used above the furnace body to ensure performance while reducing construction costs, reducing costs for enterprises.
- 3. Masonry technology of burner mouth. The burner nozzle special castable for corundum and mullite is poured into the burner nozzle of the aluminum melting furnace at one time. Convenient and fast, fully resistant to high temperature and airflow. The caliber and angle of the burner have been rigorously designed and calculated, and the use of the regenerative burner is energy-saving, environmentally friendly, and efficient.
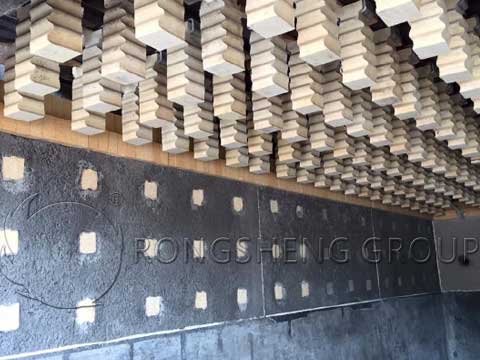
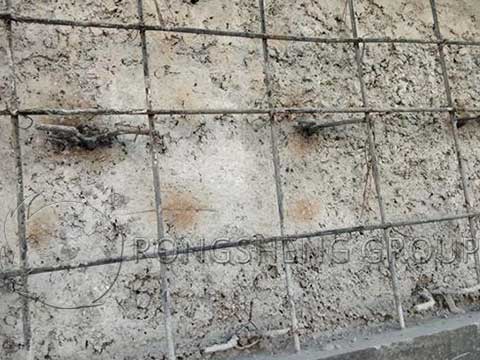
Rongsheng Refractory Manufacturer
Rongsheng is a refractory manufacturer with rich sales experience. Rongsheng’s refractory products have been sold to more than 60 countries around the world. For example, Russia, South Africa, Kazakhstan, Philippines, Chile, Malaysia, Uzbekistan, Indonesia, Vietnam, Kuwait, Turkey, Zambia, Peru, Mexico, Qatar, etc. In order to solve the refractory lining problem of various high-temperature kilns, an effective solution is proposed. It has been praised and recognized by customers, and the customer’s return evaluation rate has increased significantly. For more information about the prices and information of refractory materials for aluminum melting furnaces, please contact us. We will provide you with services according to your specific needs.