Why Use Magnesia Carbon Refractory Materials for Ladle Wall Working Lining?
When choosing refractory materials for ladle lining, the main considerations should be the use conditions of the ladle lining, the requirements for the purity of molten steel, the safety of ladle operation, and the best cost per product. In Europe, carbonaceous, alumina magnesia carbon, and periclase corundum carbonaceous refractories are mostly used as ladle working linings. When refining molten steel outside the furnace in ladle and ladle furnaces, magnesia carbon refractory materials are recommended.
Years of operating experience have shown that alumina magnesia carbon refractory materials are most commonly used in the walls of medium and large-scale ladles for converter steelmaking. Because it can ensure that the ladle lining has the best thermal physical properties. However, due to the price increase of aluminum-magnesium-carbon refractories. As well as refining molten steel in the ladle furnace and vacuuming the molten steel in a vacuum chamber, magnesium-carbon refractories are most commonly used when smelting special steel in small and medium-sized ladles.
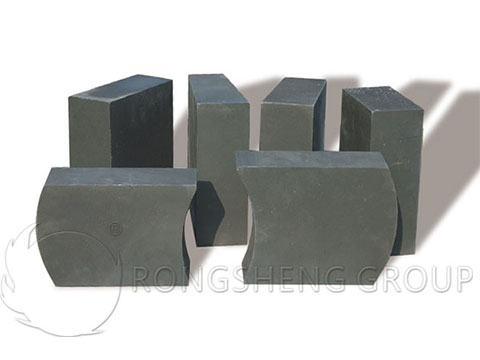
Why Use Magnesia Carbon Refractory Materials for Ladle Wall Working Lining?
After comparative analysis and observation of the use of magnesia-carbon refractory materials and alumina magnesia carbon refractory material, it is found that the following conditions all illustrate the superiority of magnesia-carbon refractories as refractory lining materials for ladle walls.
From the point of view of thermophysical properties, for magnesia carbon refractory materials, the thermal conductivity decreases as the temperature increases. For alumina-magnesia-carbon refractory materials, the situation is reversed, and the thermal conductivity increases as the temperature increases. Because for aluminum-magnesium-carbon refractories, the layered structure is not its unique phenomenon, while for magnesia-carbon refractories, the structure is its typical structure. The lining of the aluminum-magnesium-carbon refractory material does not have “pebbles” damage during use (see Figure 1).
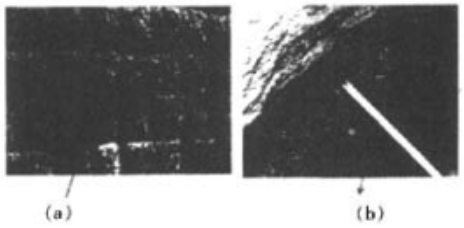
a – Magnesia carbon refractory on working lining b – Alumina-magnesia-carbon refractory on working lining
From the photo (see Figure 1, b), it can be seen that due to the best thermophysical properties and the correct choice of the chemical composition of the refractory material, there is no layered structure in the brick. Therefore, the working lining made of alumina magnesia carbon refractory materials has an integral structure. In the production of converters, electric furnaces, and open hearth steelmaking, it has been repeatedly observed that aluminum-magnesium-carbon refractory materials are used to build ladle wall linings of different capacities with similar structures.
Due to the decrease in thermal conductivity as the temperature increases, and due to the existence of a layered structure. The stress generated in the magnesia-carbon refractory material is far greater than the stress in the aluminum-magnesium-carbon refractory. That is to say, the expansion rate of the hot side of the brick is much greater than that of the cold side, especially when the carbon burns. This leads to stress on the interface of the brick, causing peeling. There is a well-known type of damage -the “pebbles” effect. Therefore, horizontal joint cracking often occurs in magnesia-carbon lining, causing molten steel to leak.
The recognized advantage of magnesia carbon refractory materials is their versatility. The refractory material can be used for both the cladding wall and the slag line area. When the supply of alumina-magnesia-carbon refractory material is interrupted, magnesium-carbon refractories can be used to replace the former. Experience in the use of refractory materials has shown that magnesium-carbon refractories with a total carbon content of nearly 15% can be used in the ladle wall of the converter steelmaking even in the molten steel zone. The use results show that the service life of the ladle is hardly reduced or slightly reduced at this time. When the joints are cracked, the molten steel is usually partially immersed in the joints of the bricks, and the bricks are bonded together, which improves the strength of the lining.
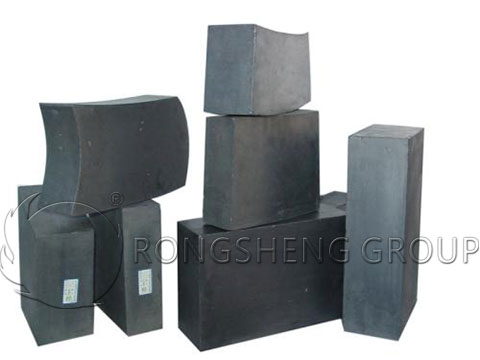
Alumina Magnesia Carbon Refractory Material for Ladle Lining
After analyzing the mutual composition and chemical composition of the two types of refractories, the following insights were obtained. The alumina magnesia carbon refractory material is made from corundum-containing raw materials (such as bauxite clinker, fused corundum, and flake alumina), to which periclase sand, spinel, and graphite are added. Due to its multi-phase composition and a large amount of impurities, the corrosion resistance of aluminum-magnesium-carbon refractories is much inferior to that of magnesia carbon refractory materials. The magnesia-carbon refractory is a three-phase system: high-grade refractory periclase sand, carbon, and antioxidants, and its impurity content is also less. In the molten steel vacuum processing device, the use effect of magnesium-carbon refractory is also good.
As the disadvantage of alumina magnesia carbon refractory materials is large heat loss, the consequence is that the molten steel being refined or transported is cooled. Therefore, it is necessary to limit the carbon content and try to use raw materials with fine pore structures. However, when the slag falls into the ladle, the aluminum-magnesium carbon refractory has lower slag resistance (especially the converter slag resistance). For example, when a certain enterprise casts 10% to 15% of the total number of molten steel in the service of a medium-sized ladle, the converter slag falls into the ladle. The wall is made of aluminum-magnesium-carbon refractory materials. At this time, the slag corrodes the refractory materials, reducing its service life by 35%-40%. In this case, the company cannot prevent converter slag from falling into the ladle. When the periclase corundum carbonaceous refractory is used for masonry in the damaged area, the cost of the clad wall is reduced by 8% to 10%, and its service life is increased by 10%.
From the point of view that the molten steel is polluted by non-metallic inclusions, magnesium oxide will not enter the molten steel during the use of the lining. The elements of alumina-magnesia-carbon refractories, especially the compounds of silicon dioxide and aluminum, can enter molten steel. Therefore, when casting special steel, it is suitable to use magnesia carbon refractory materials as the lining.
From the macroscopic structure of the two refractory materials, the typical layered structure of magnesia-carbon refractory materials leads to structural exfoliation. Especially when there is intermittent molten steel casting and often injects molten steel into the cold lining (<750℃).
The structure of refractory material strongly affects its performance. For example, in the case of magnesia particles, impurities adhere to the surface. In order to produce magnesia carbon refractory materials for ladle walls, fused magnesia and sintered magnesia produced in China are often used. Its chemical composition is as follows: MgO 96.8% ~ 97.1%; CaO 1.27% ~ 1.31%; SiO2 0.62% ~ 0.71%; CaO/SiO2=1.8~2.0. The basic mineral phase on the surface of periclase sand particles is β-type dicalcium silicate. When cooled to 675°C, the mineral transforms into the gamma-type, which has a density approximately 10% lower than the beta-type dicalcium silicate. Therefore, when this conversion occurs, the dicalcium silicate breaks down into a finely dispersed state by itself. This leads to the weakening of the bond between the periclase particles. Therefore, when using magnesium-carbon refractory materials to build the lining of the ladle, during the entire ladle service process, the number of times the lining is cooled to below 650°C shall not exceed 2 to 4 times.
Buy High-Quality Magnesia Carbon Refractory Materials at Rongsheng Refractory Manufacturers
Rongsheng refractory material manufacturer not only has an advanced refractory brick production line but also has an annual output of tons of its fully automatic monolithic refractory production line. Buy high-quality magnesia carbon refractory materials at the Rongsheng refractory manufacturer. We provide refractory lining materials and insulation materials of this quality for thermal furnace equipment in various industries. For free refractory prices, please contact us. We will provide you with refractory products that best suit your production needs according to your specific needs.