Preparation of Zircon Brick with More than 65% Zr2O3 Content
Zircon Brick with More than 65% Zr2O3 Content. The molten glass and flame-flying materials melted in the glass-melting furnace will cause certain erosion and damage to the refractory materials, which will affect the service life of the glass-melting furnace. In addition, it is necessary to avoid and reduce the pollution of the molten glass. Therefore, the choice of refractory materials also has a great relationship with the life of the glass melting furnace and the quality of the glass.
Zircon bricks for glass kilns use zircon as the main raw material, adding binders and additives. Equipped in proportion, it is fired at high temperatures after mixing, kneading, molding, and drying. Zircon bricks are classified into high-density type and dense type according to production technology and physical and chemical indicators.
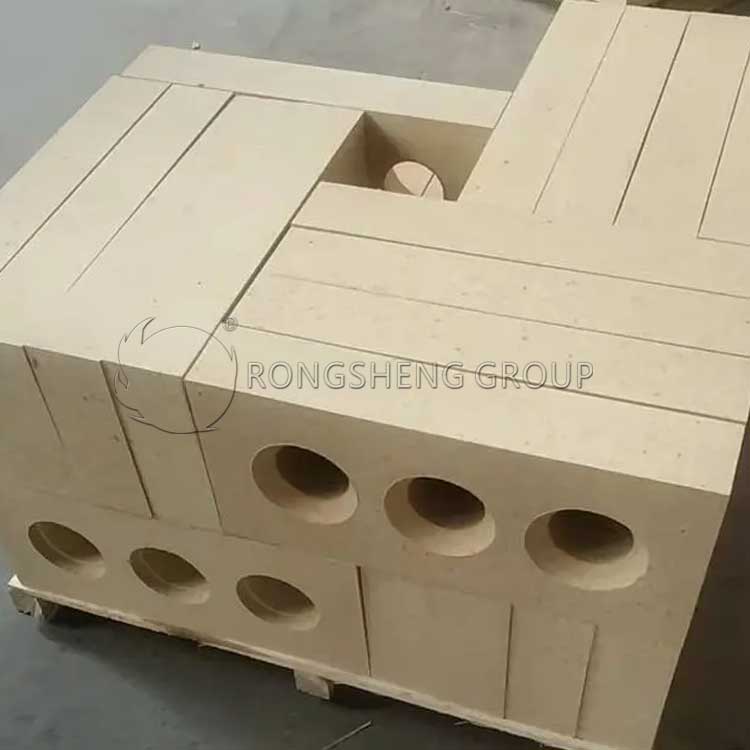
Performance of Dense Zircon Brick for Glass Kiln
- 1. High refractoriness and high softening temperature.
- 2. Strong resistance to slag liquid corrosion and strong acid resistance.
- 3. High compressive strength.
- 4. Good thermal shock resistance.
Where are the dense zircon bricks for glass kilns mainly used? Zircon bricks are used for the working layer of the glass kiln pool wall, and its density is high, as the working layer of the pool wall, it has a strong ability to resist the corrosion of the molten glass.
Preparation of Zircon Brick with Zr2O3 Content Greater than 65%
In recent years, with the advancement of glass industry technology, the application and promotion of kiln insulation technology. The consumption of machine-pressed zircon bricks containing 65% zirconia has been increasing. It is mainly used in the gaps, upper partition walls, fire viewing holes, temperature measuring holes, and other parts of the glass furnace. The temperature of this part is high and it is eroded by flying material and hot air flow, and the environment is very heavy.
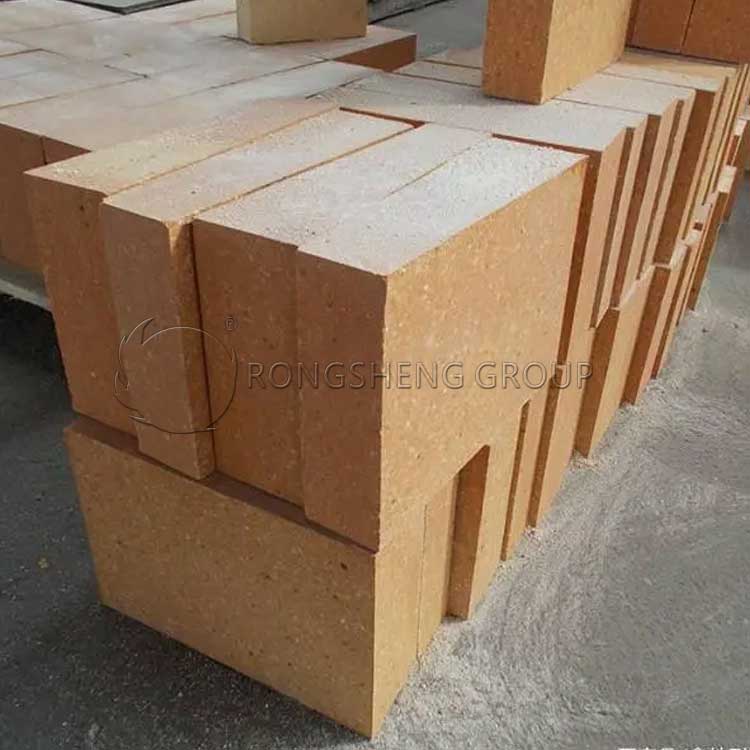
Development of Zircon Bricks
Raw material selection. To make zircon bricks with a Zr2O3 content greater than 65%, the content of the raw material Zr2O3 must be greater than 66%. The chemical composition and particle size of raw materials are shown in Table 1 and Table 2.
Table 1 Ingredients
Items | ZrO2 | SiO2 | Al2O3 | Fe2O3 | TiO2 | K2O | Na2O | MgO | CaO |
w / % | 66.25 | 32.3 | 0.35 | 0.08 | 0.2 | 0.03 | 0.12 | 0.013 | 0.05 |
Table 2 Raw Material Particle Size Distribution
Items | 0.5~0.2mm | 0.2~0.08mm |
w / % | 14 | 86 |
The raw material of zircon is in the form of sand, which cannot be directly used to make bricks and must be finely crushed. Since zircon has a large grindability index, fine powder is obtained by vibrating mill and jet mill. The particle size of the fine powder is shown in Table 3.
Table 3 Fine Powder Particle Size
Size Distribution | 30~20μ | 20~8μ | 8~2μ | <2μ |
w / % | 33 | 34.7 | 22.3 | 10.2 |
Due to the location of the zircon brick containing 65% ZrO2, the material should have good high-temperature physical properties, and the aggregate is closely related to it. The zircon sand is ground fine, and then made into a green body, which is sintered at a high temperature and then broken into different particle sizes. As the zircon material is a brittle material, the broken particles are in the form of flakes. The compressive strength of flake materials at room temperature is about 50% higher than that of granular materials. On the contrary, under the same conditions, the bulk density of granular materials is 0.12g/cm³ higher than that of flake materials on average. Taking into account both compressive strength and density performance, the crushed material must be properly treated before it can be used. The physical and chemical properties of aggregate are shown in Table 4.
Table 4 Physical and Chemical Properties of Aggregate
Items | ZrO2 | SiO2 | Bulk Density g/cm3 | Apparent Porosity (%) | Load Softening Temperature (℃) |
Indicators | >65 | 32 | 3.9~4.1 | <8 | 1700 |
Mix the batch materials on a wheel-mill mixer, trap the materials for 16 hours, and form them on a large-tonnage mill and sassafras brick press with a forming pressure of 700~1000Kg/cm³. Applying large pressure can reduce the average distance between adjacent particles and increase the contact area, which is conducive to sintering. But after increasing to a certain level, the effect is extremely insignificant. Appropriate pressure and pressurization methods are the key to solving the problem of forming barren materials.
The sintering of zircon is difficult, and its speed is slow due to solid phase diffusion at high temperatures. Adding MgO, CaO, Y2O3, TiO2, and ZnO2 can lower the sintering temperature and promote its sintering. In this sintering, 1.5%~2.75% of Y2O3 and TiO2 were added as sintering accelerators. It is sintered in a shuttle kiln with a sintering temperature of 1580~1650°C.
The decomposition temperature of zircon is 1676°C. As the impurity content increases, the decomposition temperature decreases. The high purity of raw materials is the primary condition for the production of 65% zirconia content zircon bricks with excellent properties.
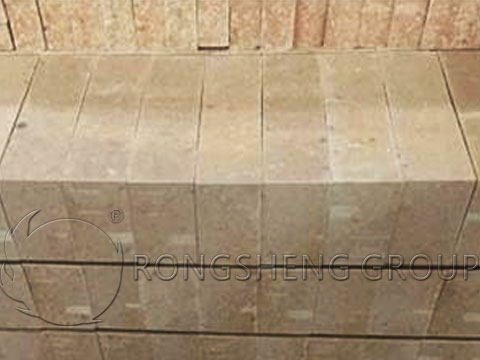
The Price of Zircon Bricks
What is the price of dense zircon bricks for glass kilns? The current price of zircon bricks in the market is around 24,000 yuan. However, before you actually purchase dense zircon bricks for glass kilns, you can consult the manufacturer in detail. The manufacturer will combine the actual situation of the kiln to provide you with the most suitable products and prices for your production needs.